Lisa Uphill always knew there was something creative she wanted to pursue as a career and couldn’t quite find her groove until hat-making came along.
It was a birthday gift from her partner Tom to attend a hat-making tutorial that set the wheels in motion and landed Lisa in her dream job.
“Monika Neuhauser (Pirongia-based milliner) taught me how to make a hat, and since then I have been obsessed. I’ve spent every spare hour that I have researching hat-making and refining my craft because I just love it so much.”
That hat-making tutorial was a little over a year ago and since then Lisa has made over 30 hats and another 10 are in production.
“I’ve traded in the Netflix for hatting,” she laughs. “I definitely feel the pull to come here (her studio) and potter with the hats.”
It was friends who made up the first of her customers but as her social media following has grown, so too has her client base, including a client in New York.
“I’m so grateful to the people who have supported me by ordering hats and showing me love on social media…it literally keeps me going.”
Lisa’s boutique hat-making business, Labour of Wild, is based in her Raglan home workshop where all the magic of bringing someone’s dream hat to life takes place.
It is here that she starts the process off with a client consult; every hat Lisa designs and makes is not only a piece of art, it also fits like a glove.
A tool called a conformer, which looks a bit like an instrument of torture, measures the exact contour of the hat wearer’s head. As Lisa points out there are universal head sizes but much like a fingerprint a person’s head will have its own unique contour.
This is one of the points of difference in a hat that Lisa makes; once finished and atop the wearer’s head it will feel like it’s meant to be there.
The 34-year-old calls herself a hat maker not a milliner. The hats she makes are similar to the traditional fedora or western hat typically worn by men, but as fashion dictates they have become popular with women over the past few decades as well.
“I consider myself to be a hat maker because I don’t make fascinators and what, typically, were women’s hats.”
Using rabbit, or sometimes the more expensive beaver felt, a hat takes Lisa around 15 hours to construct.
As well as being made to fit like a glove, Lisa spends time during the client consult talking about the design, and each hat becomes a one-of-a-kind heirloom piece with little flourishes to capture the wearer’s style.
Like the beautiful olive-green hat that has a swashbuckler design etched in the top for a client who loves pirates, or the ivory wedding hat for the bride adorned with the shell used by the groom to pop the question.
Each hat is so stunning they should be displayed as artwork when not being worn.
Like many young entrepreneurs these days, Lisa understands the importance of social media to market her brand.
Not only did her partner Tom gift the hat-making tutorial that ignited Lisa’s hatting passion, he is also the creative behind Labour of Wild branding and website.
Being a creative with a graphic design background Lisa says she was a tough customer but she put her faith in his vision for the brand.
“Tom has his design agency, which is a huge help to me. I’m aware of how lucky I am. The brand is very professional looking and I have Tom to thank for that. I know how hard it is at the beginning for a small business to afford to get a decent looking website and branding.”
In a short space of time Lisa set about purchasing the tools she needed to make great hats.
“I just knew from the offset that this was my thing. I was pretty quick to pour a lot of my savings into buying the equipment fast so that I could make life easier and do a good job. I’ve been saving for a long time and I spent probably half of my life savings on all the equipment. It wasn’t cheap but it was an investment.”
The fur felt starts out as a rough hat body which Lisa transforms using traditional hat-making methods involving heat, steam, pressure and fire.
One of the first tools she purchased was a steam iron used to saturate the hat with steam to stretch them over the hat blocks.
“I started out with a household iron and it’s possible to get by with household tools but it’s more labour intensive.”
She has also replaced a wooden spoon with a fancy tool aptly named a pusher downer which gives the brim crease a sharp definition.
“It’s a very Kiwi thing to be resourceful. Kiwis just seem to know how to do everything with what they have available, especially in small towns. So, I took on a bit of that and just tried to make do with whatever I could to begin with.”
Originally from the UK, Lisa and Tom came to Aotearoa in 2015 with their backpacks and very little else.
They came with the intention of making Raglan their home. Tom’s design agency HNDRX is set up to work remotely. Lisa started working for Stendy Electrical where she still works part-time, but hatting has become a full-time occupation. Not that Lisa’s complaining; she knows she’s found her ‘thing’. It’s what wakes her up in the morning and what she goes to sleep thinking about.
“When my friends ring or visit they know I’ll be in my studio,” she laughs.
The name Labour of Wild was born from a brainstorming session with Tom to evoke the feeling of it being a labour of love, and Lisa says, the amount of manual labour that goes into the craft. ‘Wild’ conjures up the endless design possibilities with each hat being wildly unique.
“A hat is a great vehicle for self-expression and it’s wild in the sense that it’s not the norm. It’s such an honour to be able to keep this age-old craft alive and I am so lucky to be rubbing shoulders with Raglan’s talented creative types, it’s such an inspiring community.”
By Janine Jackson
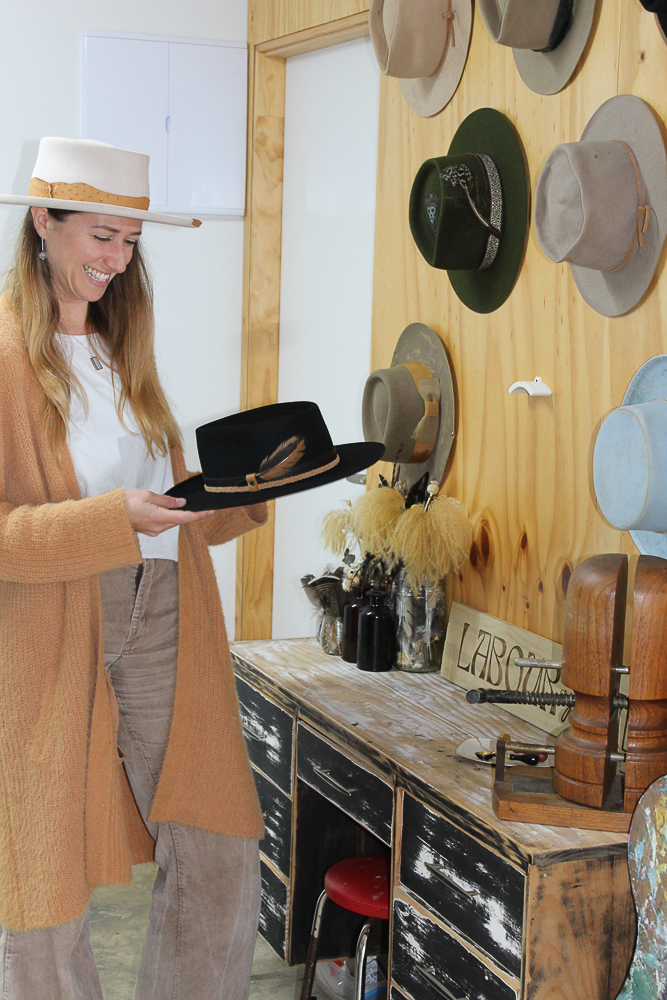